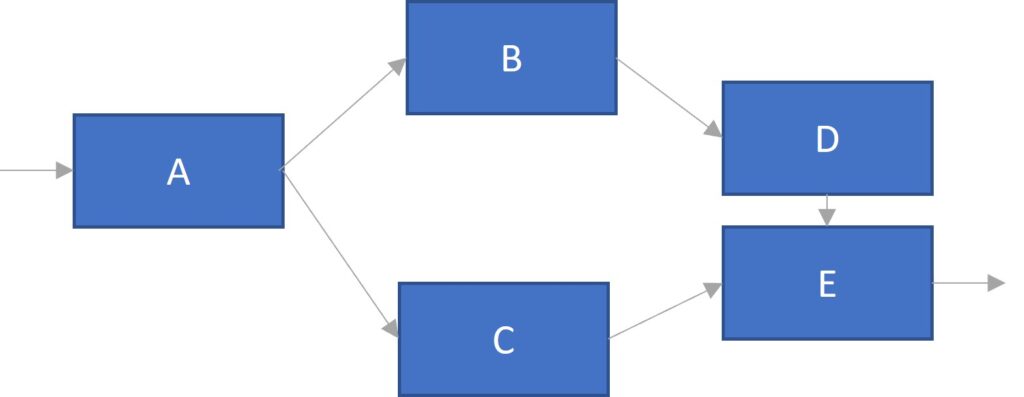
I officially started my flexible master’s programme in the autumn term of 2021 with an individual course with the final title “Simulation of Dynamics in Manning Constrained Workflows”. The overall goal was to investigate how variability impacts the relationship between cycle time and capacity need.
This post is so to speak the executive summary of my 58 page report (including appendices). At the time of writing, it has not been graded, but I do hope that my advisor and the external examiner will find it sufficient to let me pass the course… In any case, I learned a lot, which was of course the primary purpose 😉
The Plan
My work followed this plan:
- Start out with literature on dynamics in workstation based workflow
- Build a simple simulation model to use in this setting
- Move on to virtual workflows constrained only by manning and adjust the model to be able to model a case from my workplace
Variability Impact on Cycle Time and Capacity
The theoretical results for cycle time was primarily based on Hopp & Spearman’s “Factory Physics”. The references led me to the older, but excellent “Stochastic Models of Manufacturing Systems” by Buzacott & Shanthikumar. I did not read this in detail, but plan to take a further look soon. (see the Resources page for specifics on both books).
“Factory Physics” provided formulas for different situations where variability is relevant in a factory workflow. With these formulas, I now have a method to calculate cycle time of a simple, linear process given assumptions on arrival and process time distributions. For more complex workflows there were no analytical results.
Based on the results for the simple flows, the effects of variability and utilisation on cycle time could be estimated. I also built a simulation model for workstation based workflows and verified the theoretical estimated with simulation. This has given valuable insights and a much better intuition for the impact of variability. There is no doubt that there is a significant risk of underestimating capacity need, when variability is high and lead time requirements short, if one is not acquainted with these results.
I have written up the conclusions which I think every manager should know about in this article. Even if the specific formulas cannot be applied to more complex workflows, there is reason to believe that the overall findings remain valid for these cases.
Few Applicable Theoretical Results – Simulation is Required
In summary, the theory is not strong enough to handle most real-life situations, and here simulation is required. I read a lot of material on simulation. Even if I have employed different simulation methods in my work, I had not read any literature on the subject prior to the course. I will not go into details here, but expect to write a general article later about simulation approaches.
Virtual Manning Constrained Workflows
I did an analysis of how virtual, manning constrained workflows differ from workstation based workflows (where manning is assumed available at the workstation). Without going into a lot of detail, I found the following key differences:
- Worker specific process times are more likely.
- “Job memory”, i.e. dependencies on process times depending on whether the employee has performed previous tasks for the job.
- Load dependent process times are more likely.
- Capacity assumptions may be more flexible
- Higher probability of job pre-emption
- Simultaneous execution of tasks is common (or very detailed modelling of activities is required)
- Sequencing rules may be less rigid.
- The requirements to a virtual processes may be less well-defined than those for a physical process.
The Virtual Workflow Case was too Difficult
My initial ambition was to implement a simulation model which could handle all of these situations, but unfortunately, I did not succeed on that part. I did not achieve my goal of implementing a model which could be used for modelling the case.
It turned out that by removing the restrictions which a physical workstation set-up imposes on the process execution, the modelling of the execution of tasks became much more difficult, due to the increased freedom in the workflow. The problem was, that a much stronger planning algorithm was needed, and I may look into this at a later stage. Also, I think, I have a good starting point for modifying the model, to implement more of the above features, and I hope to find an opportunity to do so at some point.
It would be really cool to have a general model for simulation of virtual workflows 🙂
All the best,
Ahn Louise